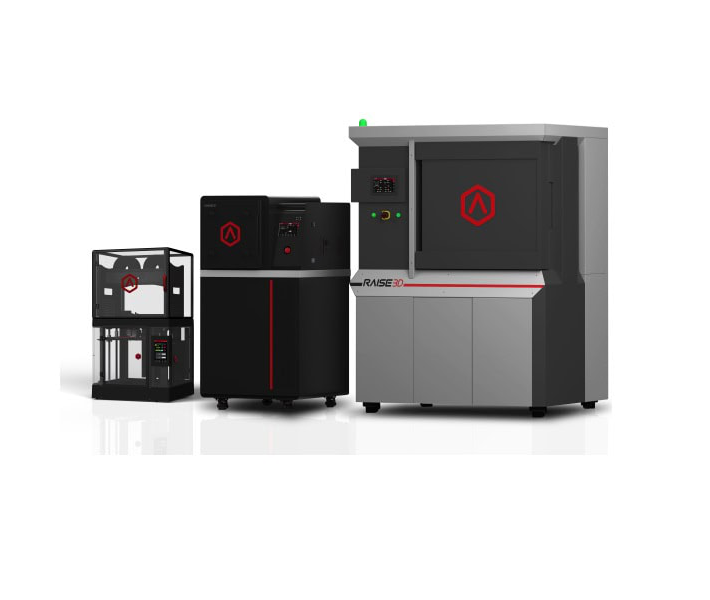
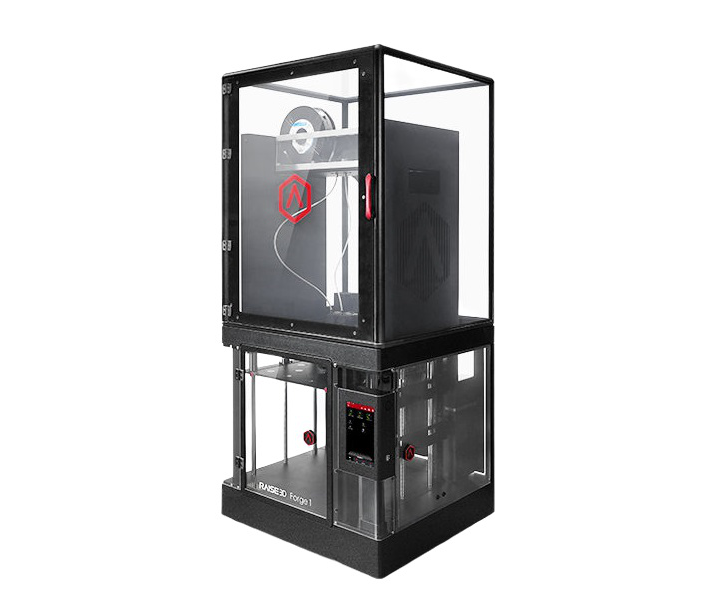
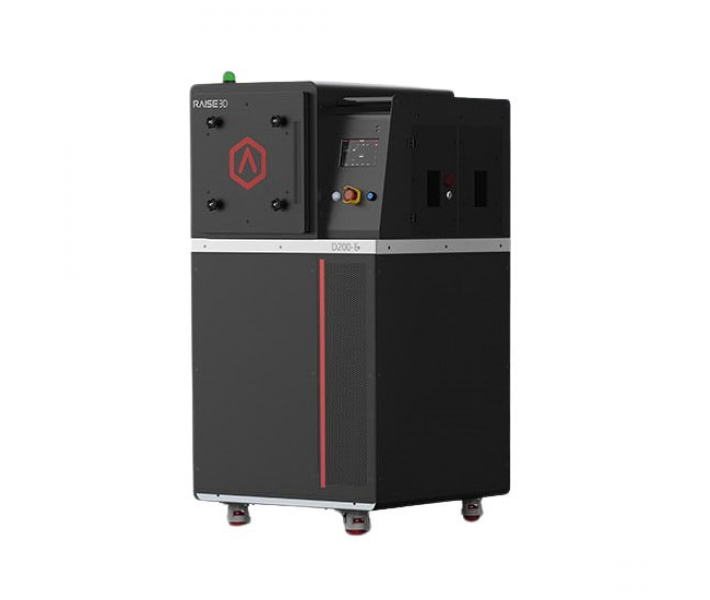



- Stock: In Stock
- Product code: 00-00012987
Metal 3D printing system Raise3D MetalFuse
Introducing a system that offers fast and affordable metal 3D printing – Raise3D MetalFuse.
The Raise3D MetalFuse system is a complete solution consisting of an indirect metal 3D printing process on the Forge1 desktop 3D printer, a catalytic debinding furnace D200-E, a sintering furnace S200-C, and a special version of the ideaMaker Metal slicer compatible with MIM equipment. The system is compatible with Ultrafuse® Metal Filaments from BASF Forward AM.
The MetalFuse solution benefits include low overhead costs and the ability to perform mass production. MetalFuse saves more energy and is more environmentally friendly than processes such as CNC and SLM (selective laser melting).
The main applications for metal parts produced by FFF 3D printing are tools, fixtures and fixtures, functional parts and prototypes, and small-scale production.
Raise3D MetalFuse advantages
Efficient and environmentally friendly process:
- Catalytic bond removal with oxalic acid is a safe and environmentally friendly method that reduces processing time by 60% and increases part density to 98% of wrought iron.
- Binder removal is the removal of residual polymer from the model, which guarantees a clean metal with high performance.
- Low-temperature sintering – further removing the binder and achieving the final hardness and strength of the part.
Cost-effective production:
- Compatibility with MIM equipment – the ability to mass-produce and scale the 3D printing farm.
- Low overhead costs – cost savings compared to traditional methods (CNC, SLM).
- Energy efficiency – energy savings and reduced environmental impact.
Cost-effective solution for printing farms:
- Custom metal parts manufacturing – flexibility and adaptability to production needs.
- High quality and reliability – printing complex parts with precision and a smooth surface.
High-quality metal filament from BASF
By using Ultrafuse® 316L and Ultrafuse® 17-4 PH metal filaments from BASF Forward AM, MetalFuse delivers better print repeatability and higher yields.
Utilizing a time-tested process
A catalytic binder removal furnace (D200-E) and a sintering furnace (S200-C) are used to further process the green parts in a process similar to that developed on the basis of BASF’s know-how from Metal Injection Molding (MIM).
Specialized slicer
The special edition of ideaMaker offers templates that are optimized for this type of printing, while taking into account the sintering and bonding processes that can be combined with MetalFuse. This special edition of IdeaMaker also features a simplified cutting process.
Safe for the environment
Filters that purify exhaust gases to a safe level and reduce pollution.
Benefits of green parts printed on Forge1
- Stable production of complex parts.
- Achieving a smooth surface of the finished part.
- Ability to print with two materials.
- Ensuring high assembly accuracy.
- Reliably copes with batch printing.
- Strength characteristics allow for outsourcing of additive removal and sintering.
The green parts produced by the Raise3D Forge1 3D printer must undergo binder removal and sintering before they are ready for use.
Print quality on Raise3D Forge1
The Raise3D Forge1 3D printer prints with a layer thickness of 0.25 to 0.1 mm, which allows for mass production of parts with smooth outer surfaces. The new method of catalytic binder removal not only reduces processing time by 60%, but also allows to increase the density of the produced parts to 97% of the level of wrought iron. The machine is equipped with a silicone heating platform with an automatic alignment system that guarantees accurate calibration. The Forge1 comes with 0.4 (default), 0.6 and 0.8 mm nozzles for all your printing needs.
Raise3D Forge1 specifications
Printing Technology | FFF |
Layer Height (micron) | 100 – 250 |
Build Field (mm) | 300*300*300 |
Build Field For Dual Printing (mm) | 255*300*300 |
Plastic Diameter (mm) | 1,75 |
Maximum Nozzle Temperature (°C) | 300 |
Number Of Extruders | 2 |
Chamber Type | Closed |
Filament Chamber Type | Closed |
Autocalibration | Yes |
Feeder Type | Direct |
Extruder Construction Type | Dual-head with electronic lifting system |
Nozzle Diameter (mm) | 0.4 (Default), 0.6 / 0.8 (Available) |
Positioning Accuracy (µm) | XY: 0.78125; Z: 0.078125 |
Print Speed (mm/s) | 30 – 150 |
Platform Heating | Yes |
Maximum Platform Temperature (°C) | 120 |
Platform Material | Glass Build Plate, Silicone |
Supported Materials | Ultrafuse® 316L, Ultrafuse® 17-4PH, Ultrafuse® Support Layer |
Running Noise, dB | < 55 dB (A) |
Air Filter | HEPA filter with activated charcoal |
Control | 7-inch Touch Screen (1024×600) |
Assembly Type | Fully-assembled |
Video Camera | Yes |
Features | Filament Run-out Sensor, EVE Smart Assistant, Power Loss Fail Safe |
Supported File Types | STL, OBJ, 3MF, OLTP, GCODE |
Operating System | Windows |
Software | ideaMaker |
Connectivity | Wi-Fi, LAN, USB port, Live camera |
Power Input | 100-240 V AC, 50/60 Hz 230 V @ 3.3 A |
Power Output | 24 V DC, 350 W |
Onboard Flash (Gb) | 16 |
Manufacturer Country | USA |
Warranty Period (months) | 12 |
Certifications | CE, CB, RoHS, FCC, RCM |
Weight Netto (kg) | 75,0 |
Dimensions Assembled (mm) | 620×626×1390 |
Operating Temperature Range (°C) | 15 – 30 |
Operating Humidity Range (%) | 10-65% RH non-condensing |
Storage Temperature (°C) | -25 to +55 |