
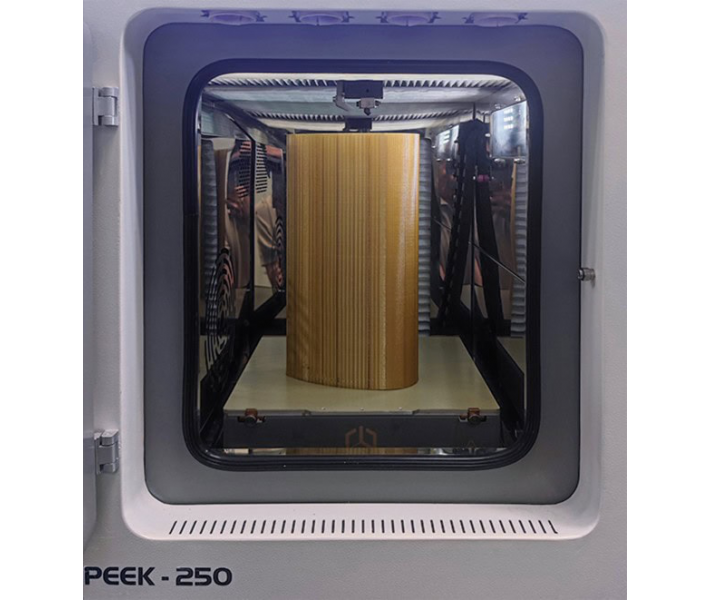
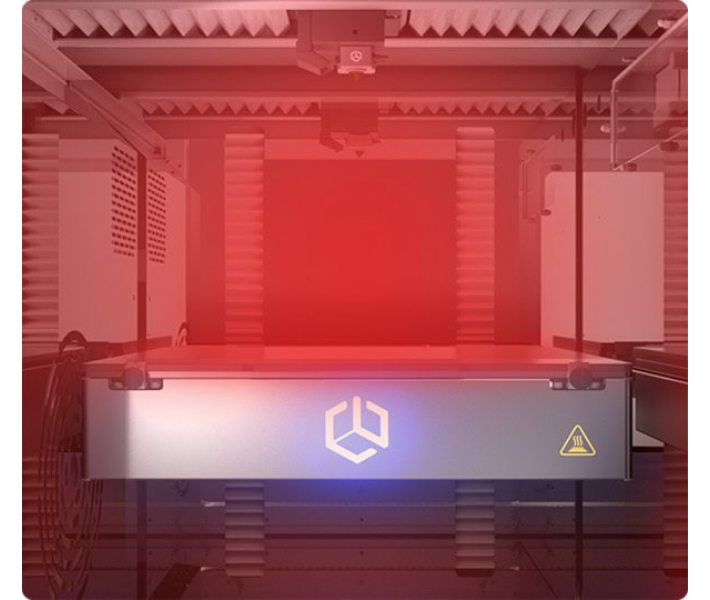
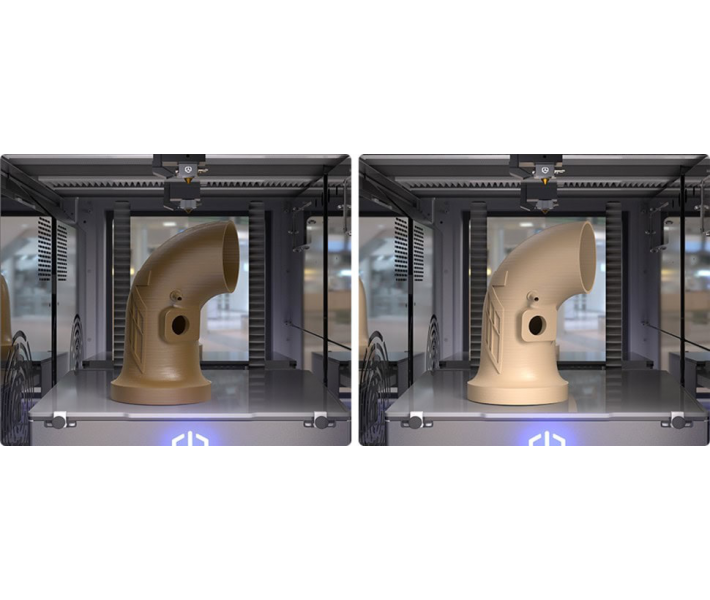
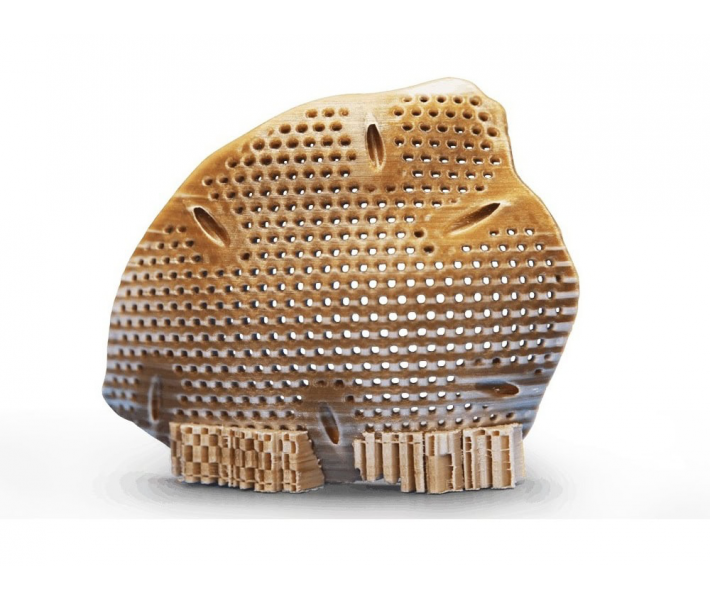
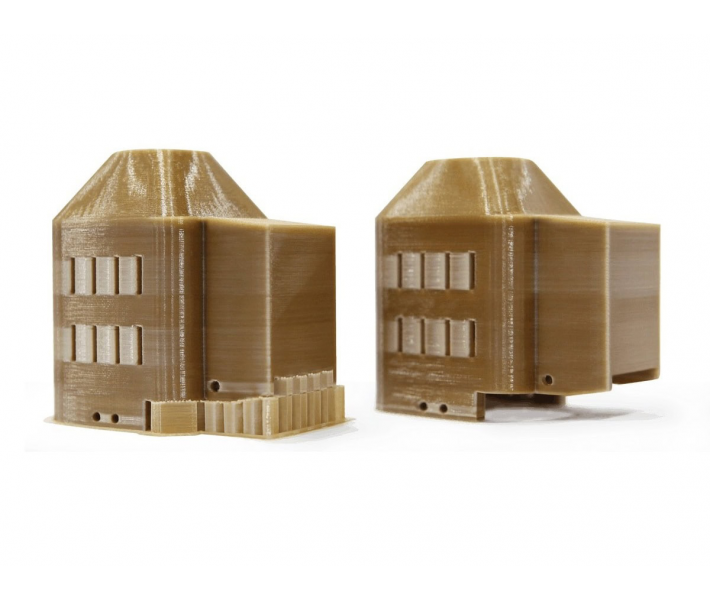
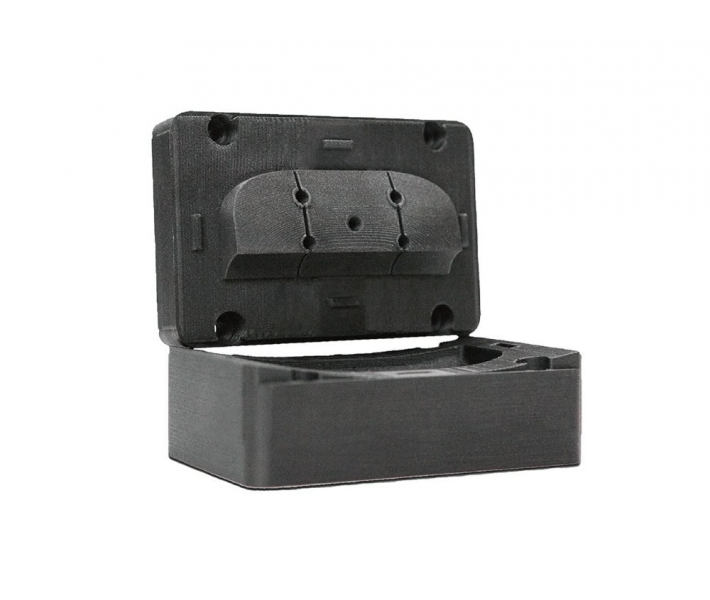
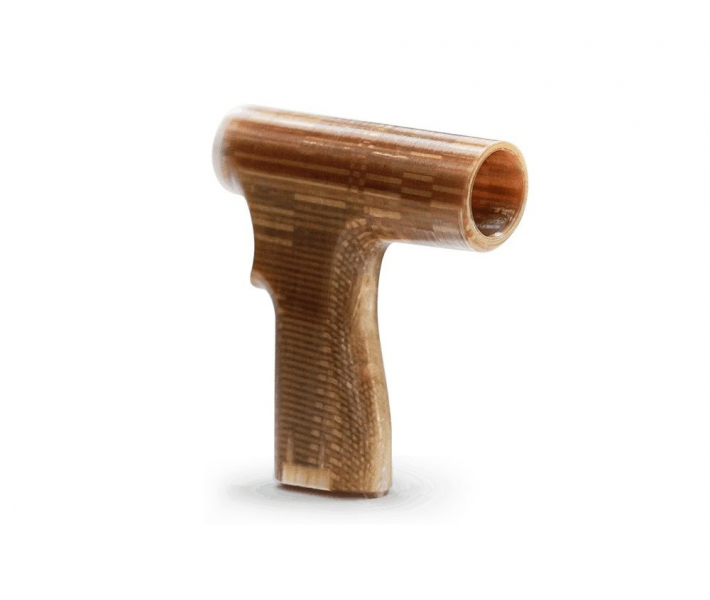
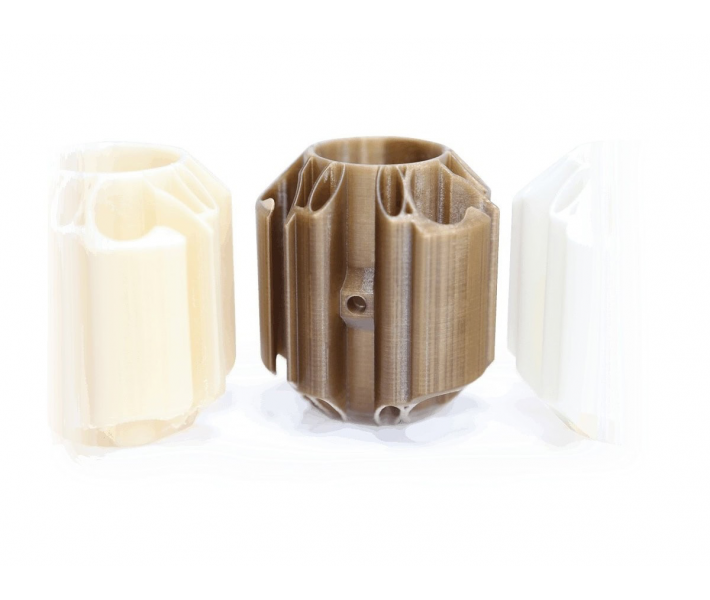
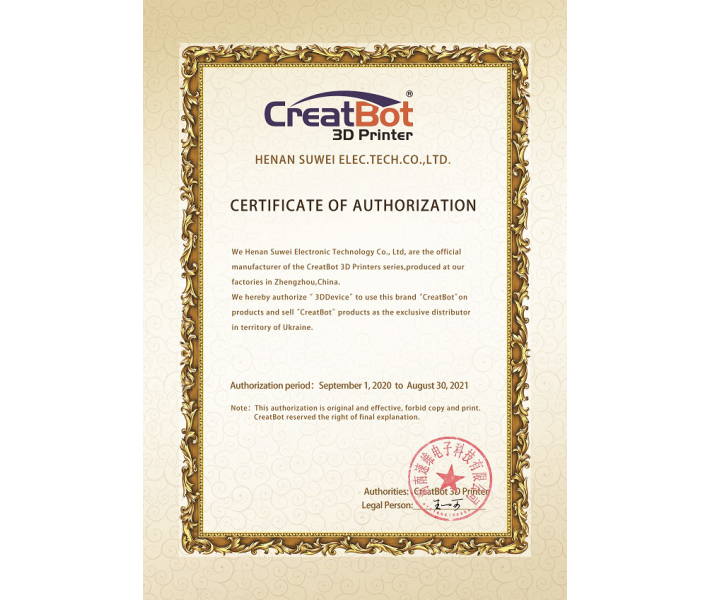










- Stock: In Stock
- Product code: 00-00011596
CreatBot PEEK-250 ultra-high temperature 3D printer
Introducing the new CreatBot PEEK-250 high-temperature 3D printer – a reimagining of industrial-grade 3D printing.
The CreatBot PEEK-250 is an innovative professional-grade 3D printer specially designed for high-temperature engineering materials. The world’s first desktop high-temperature 3D printer with a maximum hot chamber of 200°C, it excels at printing PEEK, PEI, and other high-performance thermoplastics.
Thanks to its unique design and advanced technology, it provides high print accuracy, excellent material adhesion, and a wide range of applications.
PEEK-250 key features
- Print volume – 250*250*300 mm.
- Ultra-high temperature 3D printer: nozzle – 480 °C, platform – 200 °C, chamber – 200 °C.
- Positioning accuracy – ±0.012 mm.
- Printing speed – up to 200 mm/s.
- Nozzle diameter – 0.4 mm (standard), other options are available.
- Water cooling/heat insulation system.
- When the hot chamber reaches 180 °C, the outer surface temperature is less than 40 °C (after 5 hours of heating).
- Increase the chamber temperature to 180 °C in 20 minutes.
The benefits of printing on the best professional printer
- Durable build volume. A large build volume of 250*250*300 mm accommodates large and complex parts.
- High temperature characteristics. Ability to print a wide range of engineering-grade materials: PEEK, PEI, ULTEM, CF-PEEK, GF-PEEK, PEKK.
- Excellent quality of parts. High positioning accuracy and temperature stability provide parts with excellent surface finish and strength.
- Closed chamber. Ensures temperature stability inside the chamber, which is important for printing high-temperature materials.
- Ease of use. An intuitive interface and automated processes make it easy to work with the printer.
- Unparalleled temperature control. Achieve precise temperature uniformity throughout the build chamber for unmatched part quality.
- Optimized workflow. Take advantage of automated post-processing features, such as in-chamber annealing, to relieve stress and improve part properties.
- Industrial-grade components. Engineered for durability and reliability, featuring a direct-supply extruder with high torque and advanced temperature management.
Applications
- Medicine. Production of prostheses, surgical instruments, models for dentistry, and custom-made implants.
- Aerospace industry. Prototyping of engine parts, avionics, production of high-performance components.
- Automotive industry. Manufacturing of tools, prototype parts, functional prototypes.
- Industrial design. Creation of high-precision models and prototypes.
- Research and development. Exploring new materials and applications.
Why you should choose PEEK-250?
- Highest quality parts. The high-temperature chamber ensures optimal material flow and adhesion, resulting in stronger, more durable parts.
- Save time. Eliminate the need for external annealing ovens with built-in post-processing capabilities.
- Ease of use. Intuitive controls and a user-friendly interface make it easy for beginners and advanced users alike.
Why is a 180 °C hot chamber so important?
1. An ambient temperature of 180 °C is the required temperature for annealing PEEK material.
Therefore, after the device prints the PEEK model, it can be annealed directly in the device.
Benefits:
- It is not necessary to remove the model from the platform to avoid losing the grip of the bottom of the model on the platform, which will cause the internal stress of the bottom model to lose the fixation of the platform, resulting in deformation of the bottom of the model after post-processing.
- Avoid turning off and cooling the model to remove it. There is no exchange between the hot and cold medium, which causes the model to have a large temperature difference in a short period of time, and the internal stress is fixed, and it cannot be effectively heat treated.
- After printing, the annealing treatment can be set directly inside the printer without any delay. For example, it is pre-configured to be held at 180°C for 5 hours after printing, and then held at 120°C for 5 hours to completely anneal the PEEK parts.
2. 180 °C is the temperature at which PEI material can be printed perfectly.
- Printing environment temperature requirements: generally set between 160°C and 200°C to ensure that the material can be fully extruded and bonded, and to reduce the internal stress after molding to prevent cracking. The recommended ambient temperature is 180°C to improve fluidity, obtain greater combined line strength, and improve heat resistance and chemical corrosion resistance by reducing internal molding stress.
- PEI has hygroscopic properties and can lead to material degradation. The moisture value should be less than 0.02%. The drying conditions are 150°C and 4 hours of drying, drying can be carried out directly in the cavity.
- PEI materials also usually need annealing after molding to eliminate the internal stress generated during the molding process. The advantages of direct annealing are the same as PEEK.
Why is it so difficult to raise the temperature in the chamber to 180 °C?
Thanks to the popularization of previous knowledge, we know that a high-temperature chamber is a prerequisite for high-quality molding of polymeric materials such as PEEK and PEI. But why doesn’t the chamber temperature of large industrial equipment reach 180 °C?
70-80 °C is the temperature limit for most printed circuit boards, motors, belts, and other parts. Exceeding the ambient temperature will cause these parts to break down. This is why the temperature of conventional cavity temperature printers is at this level.
120 °C is the temperature limit for high-temperature motors and belts. At the same time, they must be well cooled, shielded and insulated or heat dissipating for the circuit parts and insulating for the cavity.
150 °C requires a completely independent closed chamber design and thermal insulation design. In addition to the heat shield and heat dissipation design for all heat-resistant parts, long-term durability and heat uniformity of the heating device are also required. And the multi-layer thermal insulation design of the equipment body.
For ambient temperatures of 180 – 200 °C, an aviation-grade thermal insulation sports protective cover is also required. An excellent sports thermal insulation material can completely isolate the air under and above the nozzle, and circulate and replace the hot air collected in the upper cavity with hot air in the enclosure under balanced pressure. Ensure that the external temperature of the shell meets the safety standards for human use.
Ultra-high temperature extruder system
CreatBot PEEK-250 equipped with a two-tooth silicon carbide extruder, it has the characteristics of high torque, ultra-high wear resistance, and no step loss. It can print all filaments at temperatures below 500 °C, especially carbon fiber and glass fiber materials.
A water cooling device is required, which is the key to smooth printing of high-temperature filament. The hot-end is an integrated, wear-resistant injection molding nozzle that can be replaced within 30 seconds without removing any other parts or screws.
Thermally homogeneous 200 °C chamber
A special spoiler device allows the hot air in the cavity to circulate 360°, ensuring that the cavity is heated evenly and the polymer model crystallizes evenly at any angle and has a perfect shape.
Excellent thermal insulation and camera safety
This is the first time that an aviation thermal insulation sports protective cover has been used in professional-level equipment. With smart design, multi-channel heat dissipation, customized high-temperature resistant parts, and the use of multi-layer thermal insulation materials, when the camera temperature reaches 180°C, the temperature of the front door, top door, screen, body, and side panel of the machine is within 40°C, ensuring the safety of users.
High temperature platform 200 °C
- Ultra-flat aircraft-grade platform + polymer coating.
- Natural flatness 0.05 mm.
- High temperature flatness 0.1 mm (cavity temperature 180 °C).
- No manual or automatic alignment is required, which avoids manual alignment or sensor failure in high temperature environments.
All-in-one annealing function
After the model is printed, there is no need to remove the model from the platform, cool it naturally or anneal it in an annealing oven.
You can pre-select the “direct annealing after printing” function on the screen for the appropriate material, such as PEEK, PEI, etc. You can also change the built-in annealing temperature and time in the settings to achieve one-click annealing.
Specifications
Printing volume | 250*250*300 mm |
Filament diameter | 1,75 mm |
Number of extrudersSD | 1 |
Nozzle diameter | 0.4mm (0.3 ~ 1.0mm optional) |
Material compatibility | PLA, ABS, ASA, PC, nylon, PETG, PVDF, carbon fiber; PET-CF, PET-GF, UltraPA, UltraPA-GF, UltraPA-CF, PPSU; PEI (Full Line ULTEM™), PEEK, PEEK-CF (carbon fiber), PEEK-GF (glass fiber), PEKK, etc. |
Max. Nozzle temperature | 480 ℃ |
Chamber temperature | 200 ℃ |
Max Platform Temperature | 200 ℃ |
Best print speed | 55 mm/s |
Max. Print Speed | 200 mm/s |
Cooling | Air pump cooling and water cooling |
Platform | PCB aluminum + PEEK PCB |
Positioning accuracy | XY 0.0127mm, Z axis 0.00125mm |
Extruder | Direct drive |
Machine design | Fully enclosed hot chamber |
Special functions | Print recovery after power failure. Filament detection (pauses printing when it runs out of filament). |
Thermal insulation | Three-layer insulation + active air cooling (chamber temperature reaches 180°C, outer surface temperature less than 40°C) |
High temperature accessories | High temperature resistant motors, line rails, belts and circuits for continuous high temperature printing. |
Door cooling | Active air cooling |
Software | Creatware, Simplify3D, Cura, Slic3r |
Operating Systems | Windowsall, macOS |
Print File Type | STL, OBJ, AMF, Gcode |
Input power | 200V~240V, 20A |
Rated power | 2500W |
Screen | 7” full color touch screen, multilingual |
Connection | USB connection/USB disk |
Machine Size | 630*555*815 mm |
Weight | 120 kg |