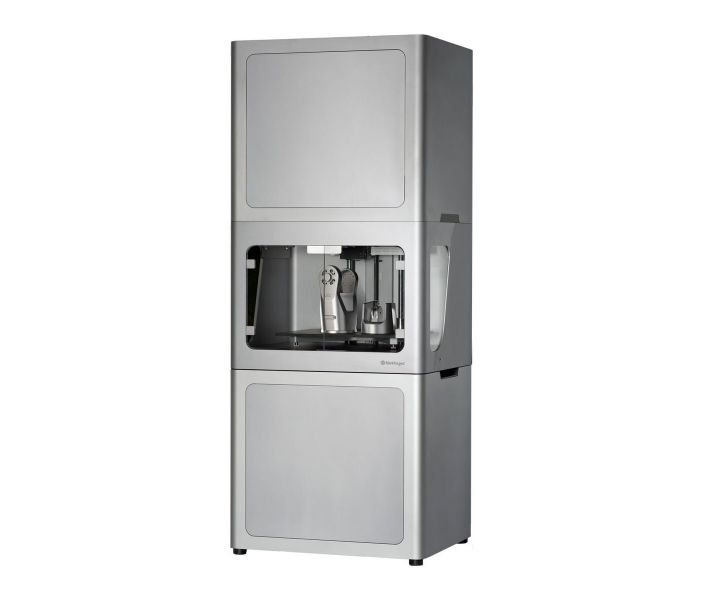
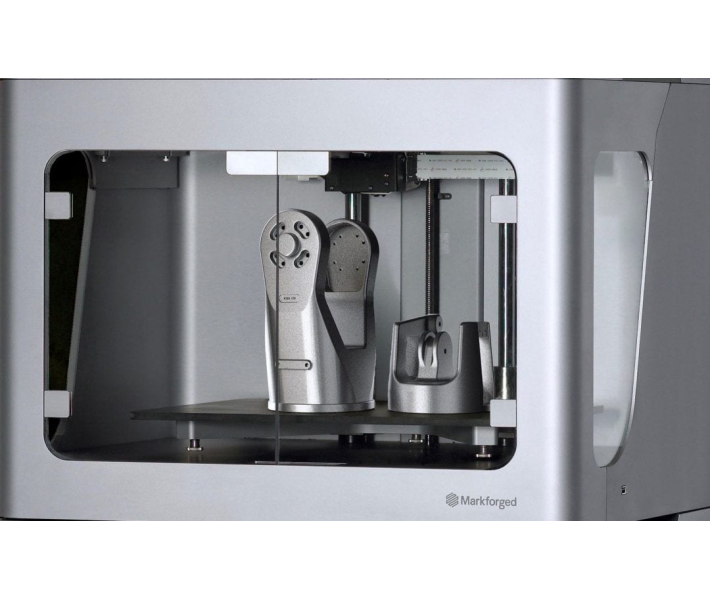
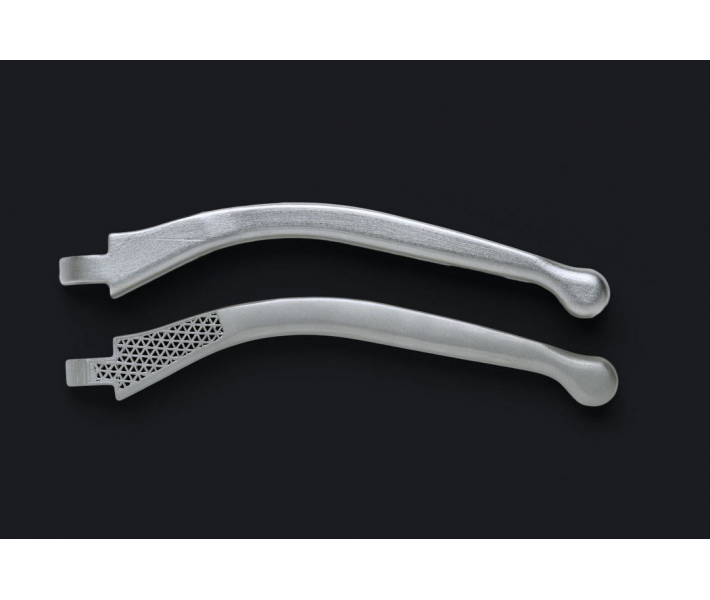
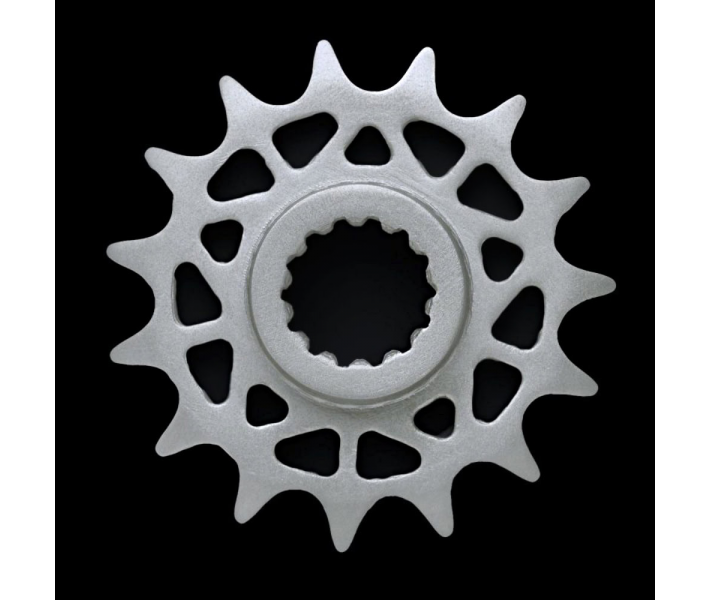
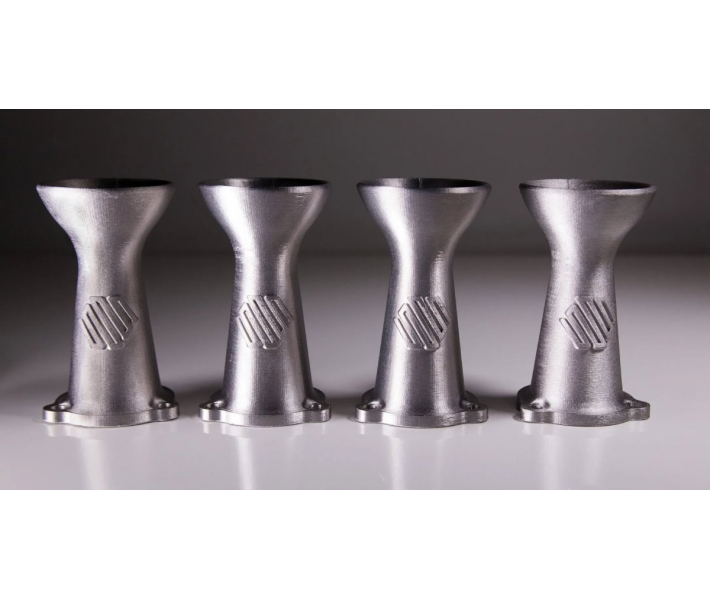
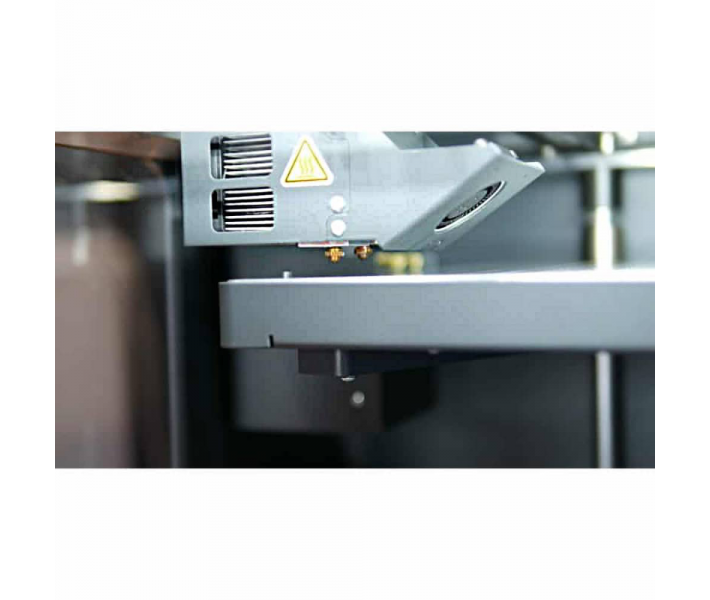
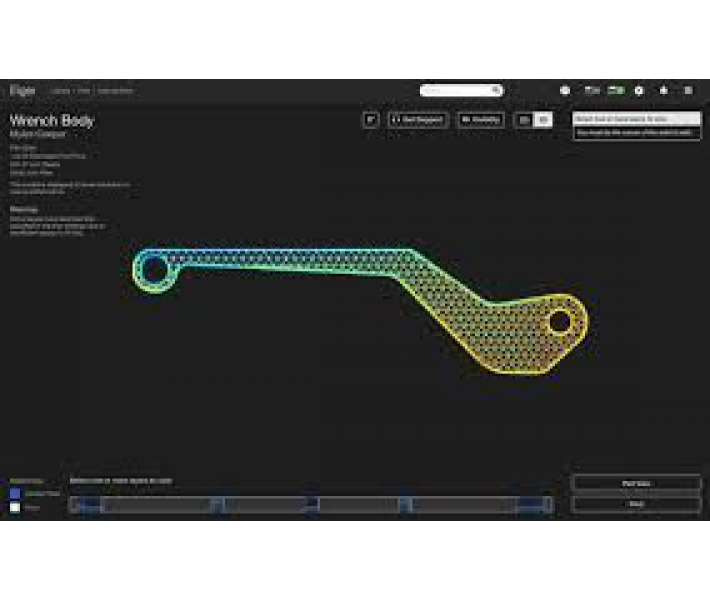
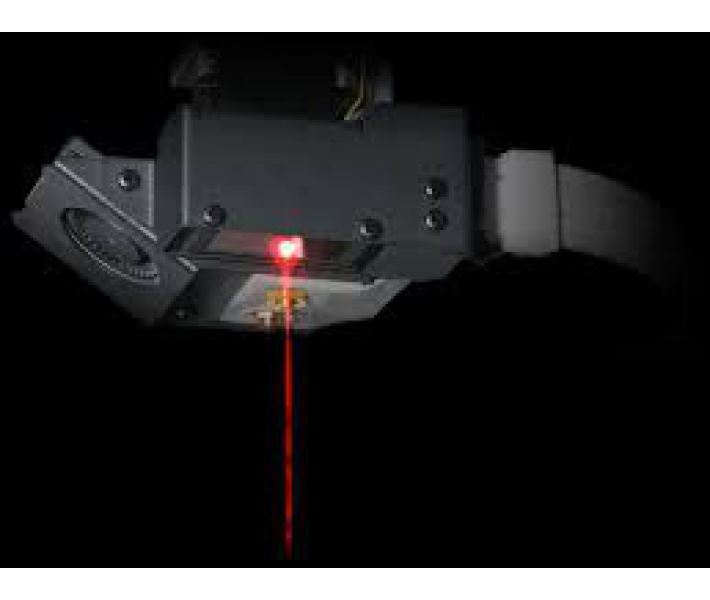
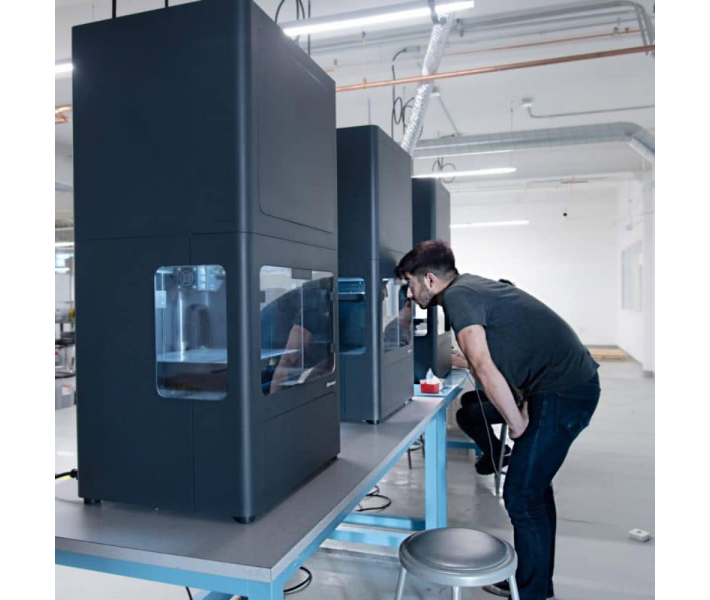
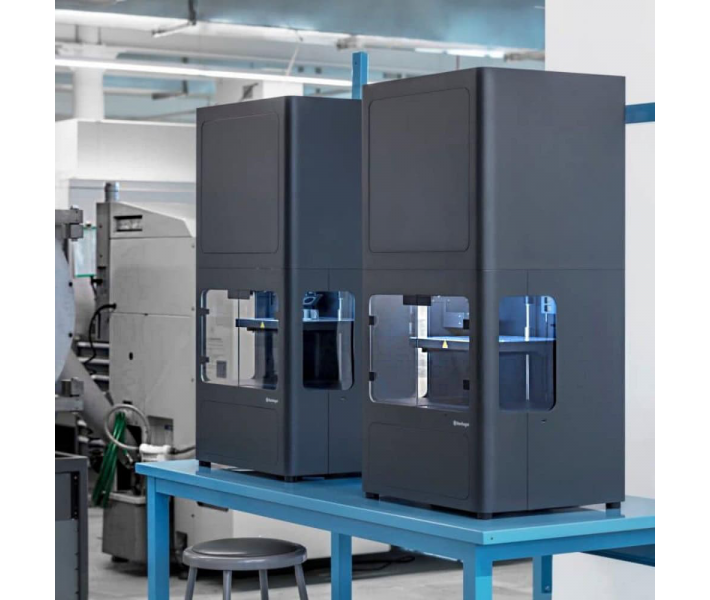










- Stock: In Stock
- Product code: 00-08800005
- Weight: 85.00kg
- SKU: 21466
Available Options
3D printer Markforged Metal X
The Markforged Metal X 3D printer is an industrial revolution in the production of metal parts.
The Metal X metal printing system is based on fourth-generation composite 3D printing technology and is a completely new type of 3D printer. By printing metal powder bonded in a plastic matrix, Markforged has eliminated the safety risks associated with traditional metal 3D printing, while enabling new features such as closed cell filling for lighter weight parts and lower costs.
How does it work?
This procedure saves time from design to printing of heavy metal parts.
- Design. Once you’ve uploaded your CAD STL file and selected the material, EIGER software does the rest, making it easy to print the part you want.
- Printing. The system prints your part with metal powder bonded to plastic, layer by layer to form the shape of your dense metal part. The parts are oversized to compensate for shrinkage during the sintering process.
- Sintering. The printed parts go through a washing stage to remove some of the binder. They are then sintered in a furnace and the metal powder is fused into solid metal.
- Ready made part. After sintering, you get a ready-to-use component made of pure metal with a density of up to 99.7%. This component can be machined and processed like any other metal part.
Wide range of metal materials
Metal X has more than five different metal materials, from stainless steel and copper to the high-temperature alloy Inconel 625, so you get high-quality metal parts the next day.
Large build space enables larger components to be printed
The large build volume of Metal X enables the automotive, aerospace and many other industries to produce major components, individual parts or spare parts quickly and inexpensively. Components are printed in a 50 micron layer, where even the smallest parts are of the highest precision.
EIGER software
Efficient production management with the browser-based Eiger software
With Markforged’s powerful, easy-to-use Eiger software, 3D metal printing has never been easier. Teams can create, manage and collaborate on parts across your entire team. Because Eiger is browser-based, you can print and manage parts anywhere you have an internet connection.
Print components with known accuracy and tolerance
Define tolerance specifications in EIGER, the included software of your cloud-based 3D printer. Your part will be scanned throughout the printing process to ensure that your needs are met at all times. If an error is detected, you will be notified and have the option to stop printing remotely to save time and materials.
Eliminate supply chain headaches
Supply chains can be unpredictable, but they don’t have to put your production needs on hold. Reduce costs and headaches by bringing metal part production in-house with the best metal 3D printer on the market. You don’t have to wait weeks or months for that vital part – you can have it the next day.
From design to usability
The Metal X system gives you the ability to print parts with a high quality surface at the touch of a button. From printing to washing and sintering, Metal X metal parts are reliable and functional for your needs.
Laser control of the construction process
Metal X is a milestone in quality and precision. With Eiger’s cloud-based software and a laser sensor on the print head, you can scan the part as it prints to ensure it meets all your requirements.
More about the Metal X metal printing system
Metal X printer
The Markforged Metal X is a new metal printer that uses a plastic die to bind metal powder, eliminating the safety risks of traditional metal 3D printers. It is safe for use in a shop environment with minimal equipment upgrades and features a precision gantry, heated chamber, print platform, and advanced extrusion equipment.
Sinter-1 and Sinter-2
The Markforged Sinter-1 and Sinter-2 are tube furnaces that are used to sinter metal parts printed on a 3D printer. The Sinter-2 is more advanced and has a larger working volume, more precise temperature control, and a mechanical door lock.
Typically, the Sinter-1 and Sinter-2 have a working time of 26 to 31 hours. However, the Sinter-2 can process small parts in express mode, allowing you to sinter up to 250 g of parts in a quick 17 hours.
Wash-1
Wash-1 is a solvent-based bonding removal system that uses Opteon SF79. Opteon SF80 or Tergo Metal Cleaning Fluid can be substituted if necessary. Wash-1 operates with simple ventilation and has a clear user experience. The Wash-1 system has been tested and confirmed as a safe system for the shop.
Specifications
Printing Technology | Metal FFF |
Building Area (mm) | 300*220*180 |
Number of Extruders | 2 |
Build Chamber Type | Enclosed |
Chamber Heating | Yes |
Auto Calibration | Yes |
Layer Height (microns) | Metal: 85-170 (after sintering) |
Extruder Design Type | Two nozzles – metal material and discharge material |
Leveling System | Automatic bed leveling, adaptive bed leveling |
Platform Heating | Yes |
Platform Material | Precision machined aluminum. Replaceable print sheets |
Supported Materials | Stainless steel 17-4PH, copper, tool steel H13, Inconel 625, tool steel A2 and D2. Support material: Ceramic – turns to powder during the sintering process |
Features | Modular design. Laser micrometer and visual module scan parts for accuracy. Plastic Missing Detection, Fiber Missing Detection, Fiber Jam Detection, Adaptive Bed Leveling, Auto Bed Leveling, Micron Precision Linear Encoders |
Software | Eiger Cloud |
Connection | Wi-Fi, Ethernet |
Power Requirements | 100-120/200-240VAC (12A/6A), IEC 60320 Type C20 |
Country of Manufacture | USA |
Certificates | UL 2011/CSA C22.2#301 Certified, CE Marked, Complies with EU Machinery Directive |
Net Weight (kg) | 75 |
Net Dimensions (mm) | 575×467×1120 |