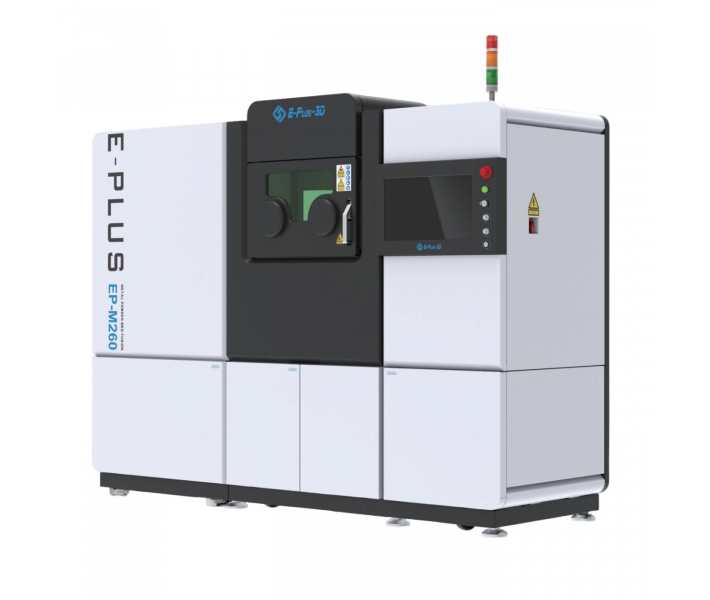
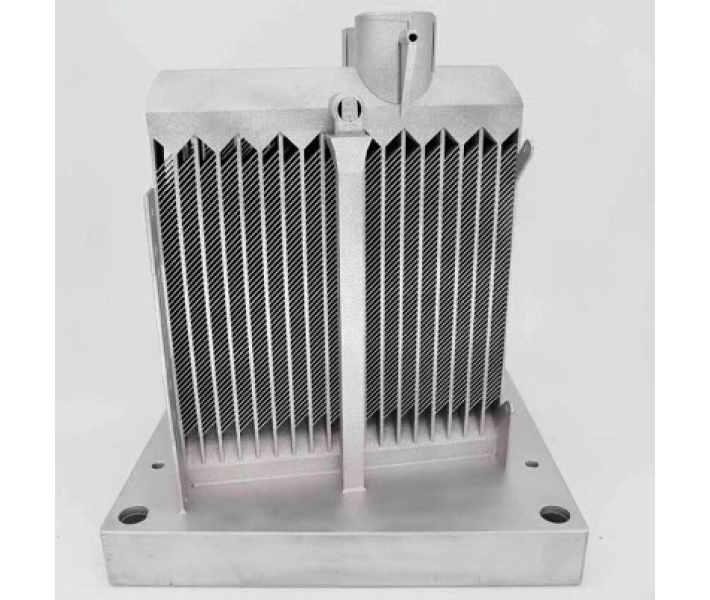
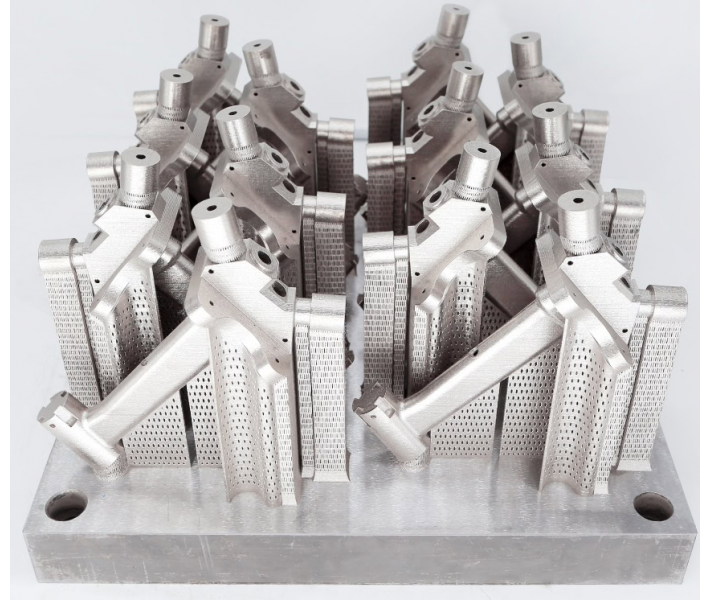
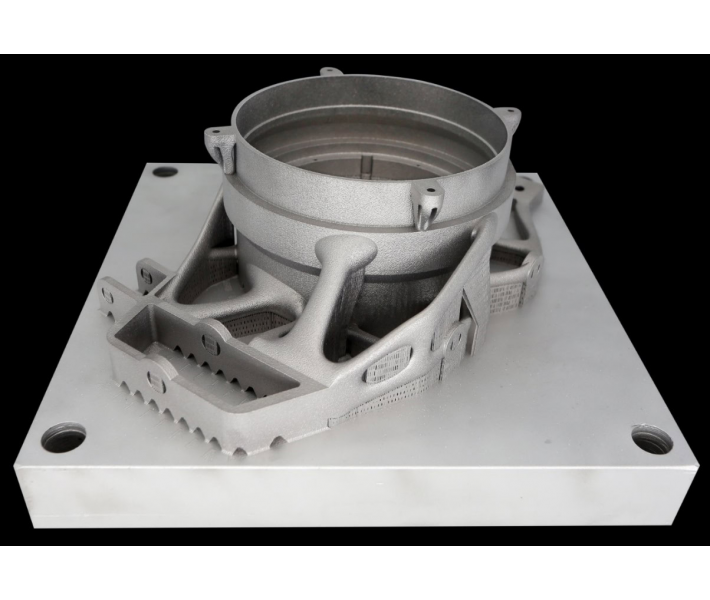
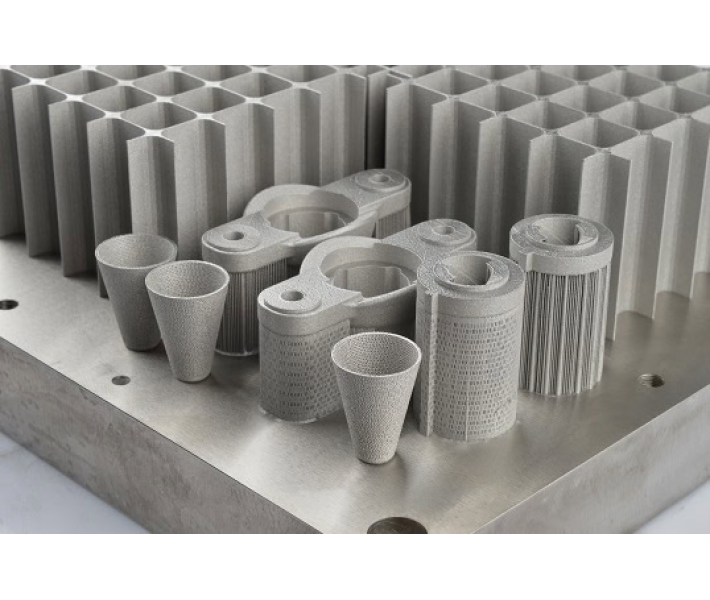





3D printer SLM E-PLUS 3D EP-M260
- Stock: In Stock
- Product code: GEN-86368795
Based on 0 reviews.
-
Write a comment
₴0.00
Ex Tax: ₴0.00
Quantity:
SLM 3D metal printer EP-M260
In the 3DDevice online store you can buy the EP-M260 metal 3D printer, which offers highly efficient and large-scale production from metal powder.
This is an industrial 3D printer that was created on the basis of the previous generation EP-M250 and received a number of new features and improvements for safer and more convenient production of high-quality metal parts from powdered metal materials.
Main features
- Build size – 260*260*390 mm.
- Power – 500 / 700 W (one or a pair of lasers to choose from).
- Optimized re-coating strategy reduces coating time.
- Software: EPControl, EPHatch.
High technology for high performance
- Innovative gas flow control and an optimized filter system ensure a stable working environment.
- The perfectly sealed chamber optimizes the oxygen content.
- Precise quality control of the laser beam.
High productivity
- Dual laser system equipped with a 260*260*390 mm collection chamber.
- Does not interrupt work during filter change.
- Optimized recoating strategy reduces coating time.
Reliable and easy operation
- Convenient powder handling systems and a glove access structure minimize contact with the powder.
- Intelligent software ensures less human intervention.
- Real-time monitoring of the production environment and construction process.
Low cost of operation
- Quantitative powder feeding and coating ensure less powder waste.
- Advanced filtration system significantly increases filter life.
- Low inert gas consumption during purging and operation.
Safe internal access through gloves
- Intelligent electronic lock without manual operation.
- Double mechanical lock for increased security.
- Signal when the access door is opened abnormally to increase the safety of use.
- Double-handle access door design allows operation without opening the door.
- Tension seal with good sealing performance, can be controlled both automatically and manually.
What’s new in the EP-M260 metal printer?
Comparison with the previous model EP-M250:
EP-M250 | EP-M260 | |
Build Volume(X*Y*Z) | 258*258*350 mm | 260*260*390 mm, larger building volume |
Wind field | – | Re-adjusted wind field to ensure uniform wind field across the entire print area and consistent printing performance |
Gas circulation filtration system | – | Increase the function of blowing back dust during printing |
Galvanometer | – | Re-adjust the structure of the galvanometer to ensure that the temperature of the galvanometer is uniform and stable, so that the laser will not have thermal drift |
Industrial computer operation mode | Mouse | Touch screen |
Gas circuit modification | – | Ensure that the chamber pressure is stable at about 25mbar |
Fan | High pressure fan | High pressure fan + Vacuum pump Shorten the inflation time |
Grating ruler | – | Increase the grating ruler to make the Z-axis repeat positioning accuracy more accurate |
Passivator | – | Use passivator to ensure safety when replacing the filter element |
Powder bucket | – | The powder bucket can be filled with protective gas in advance to ensure that no air oxygen enters the cabin when the powder bucket is replaced during the printing process |
Filtration system | Normal filtration system | Upgraded to permanent filtration system, not only extending the service life of the filter but also avoiding risks of replacing the filter. |
Self-developed software | – | Optimized data preparation software EP-Hatch |
Technical characteristics
Machine Model | EP-M260 |
Build Volume (X*Y*Z) (height incl. build plate) | 260*260*390 mm |
Optical System | Fiber Laser 500 W / 700 W (single or dual-laser optional) |
Spot Size | 70 – 100 μm |
Max Scan Speed | 8 m/s |
Theoretical Printspeed | Up to 55 cm³/h |
Layer Thickness | 20 – 120 μm |
Material | Titanium Alloy, Aluminum Alloy, Nickel Alloy, Maraging Steel, Stainless Steel, Cobalt Chrome, Copper Alloy, etc. |
Power Supply | 380 V, 50 / 60 Hz, 5 / 6 kW |
Gas Supply | Ar / N₂ |
Oxygen content | ≤ 100 ppm |
Dimension (W*D*H) | 2800*1300*2410 mm |
Weight | 2300 kg |
Software | EP Control, EPHatch |
Input Data Format | STL or other Convertible File |
Service and warranty information:
Training
- Training (including software training, operation training, safety training, maintenance training, etc.) for technicians or engineers: Technicians from our subsidiary in Germany provide on-site training for your engineers when the first metal printer is required to be installed. It usually takes 5 working days for installation and on-site training (Poland only).
- Our professional technicians can provide remote training for engineers of customers from Ukraine before installation. After that, our technicians can also offer you remote installation.
Warranty
- The standard warranty period is one year.
During this period, our technical team provides free online support for daily operation.
If the printer’s wear parts or components encounter problems during normal operation, the manufacturer will offer free replacement parts.
If problems cannot be resolved through remote support, the company can send technicians to the customer’s site.
After the warranty period, regular maintenance of the equipment is recommended. - We recommend regular maintenance of the equipment to ensure that it is working properly, and the recommended interval between each maintenance is 1 year.
Usually, regular system maintenance is performed by our specialists, and they will provide you with a detailed maintenance report after the service is completed.
To clarify the price of maintenance, please contact your manager.
Buy a metal 3D printer in Ukraine at an affordable price
Printer Settings
Build Volume (X*Y*Z) (height incl. build plate)*
Build Volume(X*Y*Z)
Dimension (W*D*H)
Fan
Galvanometer
Gas circuit modification
Gas circulation filtration system
Gas Supply*
Grating ruler
Industrial computer operation mode
Layer thickness*
Machine Model
Material
Passivator
Powder bucket
Printing Accuracy (µm)*
Self-developed software
Source of power
Theoretical Printspeed
Wind field
Details
Software
Weight and Dimensions
Weight Netto (kg)*